Modernisation and innovative development projects
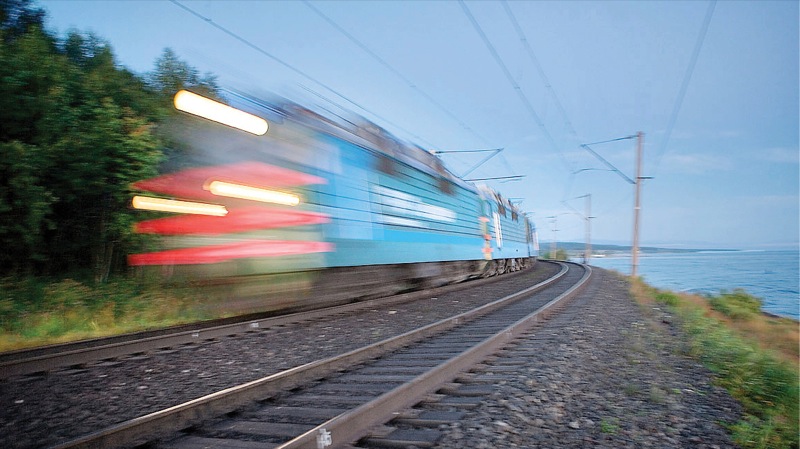
The Company spent a total of RUB 1.1 bln on scientific and technological development in 2014, or 74.2% of the amount spent in 2013.
New technologies
The Luzhskaya-Marshalling station began automating shunting technologies in the reporting year using automatic switching equipment developed by Siemens and integrated with the Russian marshalling station management system jointly with Russian centralisation systems and the automatic train shunting control system.
The introduction of this system will make it possible to try out new technology on the railway network for hazardous second-class freight, while reducing railcar processing costs by 5%, doubling labour productivity, ensuring shunting processing capacity of 5,000 railcars per day, reducing energy consumption 25% and ensuring traffic control accuracy of 0.1 km/h for hump engines.
Import substitution
Jointly with Italy’s ECM Safety Solutions and Technology, the Company is setting up a multi-station microprocessor centralisation system with an integrated automatic blocking system. This marks the first time a project is being implemented in accordance with Russian regulatory safety requirements and has open-source software and a computer-aided design system.
The system will feature a high level of adaptability and its life cycle cost will decrease by 20% compared with the currently imported microprocessor centralisation systems.
Establishment of new generation locomotives
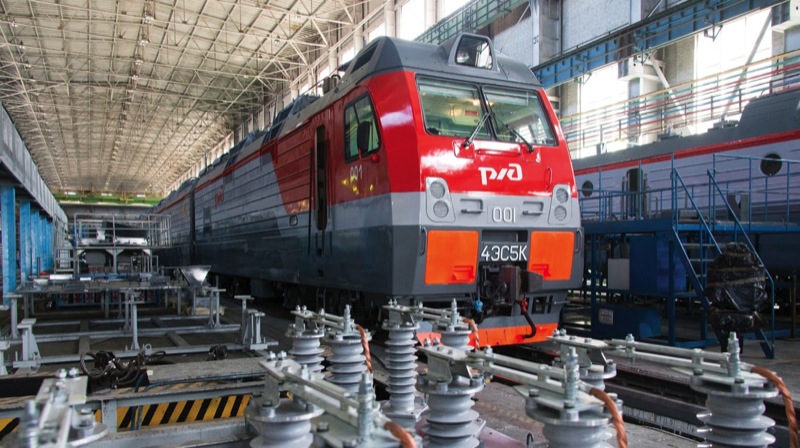
The Company continued establishing new generation locomotives in the reporting year. Certification was completed for the 2ES5 Skif and 2ES7 innovative new generation mainline electric AC freight locomotives with asynchronous traction motors, and a certificate was obtained in November for the most powerful electric freight locomotive in the world — the 4ES5K. These electric locomotives are designed to carry heavy haul trains weighing up to 9,000 tonnes. Acceptance tests were conducted on the TG 16M mainline diesel locomotive that is to run on Sakhalin Island and is designed to operate on both
Innovations in infrastructure
One of the key areas of the Company’s scientific and technological policy is the introduction of innovations in infrastructure, where expenses on shipping activities make up approximately 35% of the total volume. A key priority is to reduce the cost of the life cycle of facilities while ensuring the safety of the transportation process and a high level of reliability of technical equipment.
The testing of new turnouts for heavy haul traffic was conducted for the first time in Russia at the Orekhovo-Zuyevo station in the reporting year jointly with the company Vossloh. The turnout is designed for freight cars with a
The Company began comprehensive testing at the Shcherbinka experimental ring on four types of ballast-less track structures for high-speed mainlines and the combined traffic of manufacturing companies from Russia and EU countries.
The first complex to monitor the infrastructure of BAM created on the core of the 2TE116 diesel locomotive marked a new stage in the development of mobile diagnostic tools. It replaces several diagnostic infrastructure railcars and inspects tracks with a load of up to 24 tf. In December 2014, the complex was transferred to the Far Eastern Infrastructure Directorate. The annual economic effect from its use is valued at more than RUB 26 mln.
An analysis of the development prospects for diagnostic tools revealed the need to equip the infrastructure for Sapsan high-speed electric locomotives with diagnostic complexes. Russian specialists are building an innovative on-board diagnostic system that evaluates the infrastructure of the St Petersburg-Moscow line according to 76 parameters. This will lay the foundation for fundamentally new technologies of the 21st century that radically alter the structure of diagnostics tools and greatly improve the efficiency and reliability of the information obtained.
Introduction of RRMRA methodology (Resource and Risk Management and Reliability Analysis during life cycle stages)
The Standard of Resource and Risk Management and Reliability Analysis during lifecycle phases was developed to form a list of reliability and functional safety indicators that are given when preparing technical requirements for systems, devices and equipment used on Russian Railways infrastructure.
The approaches to reliability and functional safety applied in the standard focus on the relationship between the reliability and functional safety indicators of the infrastructure and the cost of its life cycle. According to the approach, an increase in initial expenses during development (manufacturing/ procurement) may lead to improved reliability and/or reparability of the facility and, consequently, thus increased availability, which results in decreased operating and maintenance (repair) expenses.
Therefore, the requirements for reparability mainly include time and labour expense indicators that are essential to assessing the cost of ownership or the cost of the life cycle as a whole.
At present, ten interstate and national standards have been developed along with 14 corporate standards and more than 60 methodological documents for different businesses.
One example of the effectiveness of the newly introduced system is the method developed by Russian Railways and introduced throughout the
Oversight Service and more than 13,000 were rejected at technical inspection stations. This made it possible to reduce the number of side frame fractures by more than 66% in 2014 compared with 2013.
At present, the Company is in the final stage of preparing a regulatory framework to determine the physical wear of infrastructure facilities. The RRMRA indicators are already being utilised when preparing requirements for the procurement of products or Russian Railways.